Anthracite, often referred to as hard coal, is unique to 5 counties in northeast Pennsylvania: Lackawanna, Schuykill, Northumberland, Luzerne, and Carbon. The area represents approximately 484 square miles that overlaps part of the Route 6 Corridor.
In Lackawanna County, the history of anthracite can be learned at the Pennsylvania Anthracite Heritage Museum in Scranton. The museum tells the story of hard coal mining and related industries as well as the story of the immigrants who came here to work in these industries. Recently, while perusing our archive of historical stories, we came across these two sections about anthracite and iron. The following is a short history of these resources in Pennsylvania and how they helped shape the PA Route 6 Heritage Corridor.
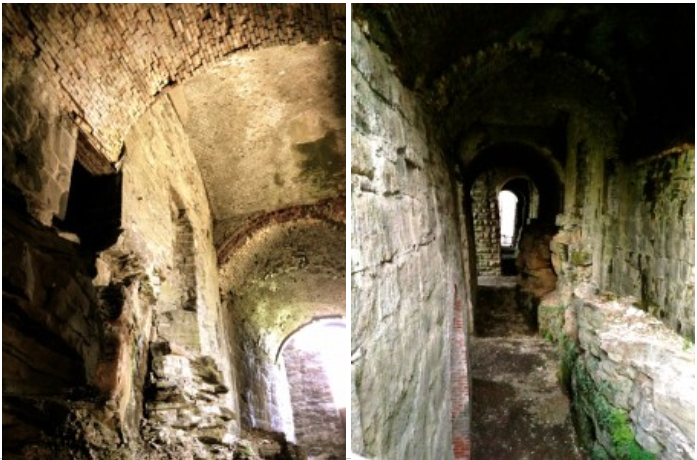
Tunnels in abandoned anthracite mines. Visit the Pennsylvania Anthracite Heritage Museum to learn more about the importance of anthracite in the history of this region.
Anthracite
The discovery of anthracite was as early as 1762 by Connecticut settlers in the Wyoming Valley. Local blacksmiths discovered that it was a reasonable fuel for metalworking by 1769, but it was not recognized as a refining fuel until the early 1800s. Philip Ginter is often credited with the first documented discovery of anthracite on Summit Hill near present day Jim Thorpe. Ginter gave a sample of the coal to Jacob Weiss, who sent it to Philadelphia for analysis. Recognizing that there was some value, Weiss, Charles Cist, John Nicholson, and Robert Morris organized the Lehigh Coal Mine Company in 1792. (37)
In 1814, William Wurtz, a Philadelphia merchant, acquired large tracts of coal land in northeastern Pennsylvania and founded the town of Carbondale. David Nobles, a local hunter, brought samples of the coal to New York and Philadelphia for appraisal. In the winter of 1822, William’s brother, Maurice Wurtz, mined 800 tons of coal and sent part of it by sleigh to the banks of the Lackawaxen River for loading onto rafts. Within a few years, the Delaware & Hudson Canal Company acquired the mines and adjacent property. The settlement at Carbondale grew rapidly as Irish and Welsh miners found work there. (38) By the 1870s, the D & H had gained control of many mines and towns throughout the region, including Archbald (1846) and Mayfield (1874).
Josiah White and Erskine Hazard burned anthracite in the forges of their Fairmount Nail and Wire Works near Philadelphia in 1812. Impressed with its qualities, they took a 20-year lease on some coal lands near present day Jim Thorpe, Pennsylvania (39) in the Lehigh Valley. In 1820, White and Hazard constructed a canal to ship coal, and by 1828, the Lehigh Coal & Navigation Company was already expanding. In the 16 years since its introduction in Philadelphia, annual consumption had jumped from zero to 77,395 tons. After 1837, anthracite was the primary fuel for smelting iron. (40)
Until about 1870, immigrant miners from Ireland and northern Europe worked the coalfields. As the mining operations expanded, and new mines were opened, coal operators found new pools of workers in the poor peasants of central and southern Europe. The new miners were willing to work for lower wages, and bitter conflicts erupted as the newcomers began to replace the older miners. (41)
Iron
By the 1830s, it was clear that anthracite could efficiently be used not only to refine iron, but also to smelt it. In 1825, the Franklin Institute in Philadelphia had offered a prize to the first person to smelt a commercially viable quantity of iron using anthracite. The prize was a catalyst to research and development, and within the next decade, experimental ironworks were established throughout the Lehigh, Schuylkill, and Susquehanna valleys. (42)
Prior to the use of anthracite, iron was smelted using charcoal. An extensive iron industry developed in the early years of the 19th century in central Pennsylvania. In the northeast, deposits of iron ore were also known, and as early as 1799, attempts were made to produce iron.
Ebenezer and Benjamin Slocum purchased a large tract along Roaring Brook, near its confluence with the Lackawanna River in 1798, near present Scranton. The tract became known as Slocum Hollow, and within a year they began to smelt and refine small quantities of iron at the bloomery forge they’d constructed there. They operated the bloomery until 1826. The forge lay idle and fell into ruin until 1840, when it was acquired and developed by Scrantons, Grant & Company. Through the 1840s, the company endured start-up miseries and several reorganizations, but eventually specialized on the production of T-rail (43) for the new railroads under construction throughout the region. (44)
Current Uses and Mining
Because anthracite burns so much cleaner than regular coal, it is most frequently used nowadays in hand-fired stoves or automatic stoker furnaces. It delivers the highest “energy per its weight” and produces little soot, which makes it ideal for home use. However, anthracite costs approximately two to six times more than regular coal.
Today, anthracite accounts for about 1% of global coal reserves. In 2020, total world production of anthracite was approximately 615 million tons. Only a handful of countries mine for it: China, Russia, Ukraine, North Korea, South Africa, Vietnam, the UK, Australia, and of course the United States. The largest known deposits of anthracite in the world, with an estimated reserve of seven billion short tons, is located in the coal region of Northeastern Pennsylvania, which includes Lackawanna County, in the PA Route 6 Heritage Corridor.
Sources:
(37) Anthracite Trust (Freeman, 1994), page 91.
(38) Pennsylvania: A Guide to the Keystone State (WPA, 1940), page 360.
(39) Formerly, Mauch Chunk.
(40) Pennsylvania: A Guide to the Keystone State (WPA, 1940), page 75-76.
(41) Pennsylvania: A Guide to the Keystone State (WPA, 1940), page 336.
(42) Anthracite Trust (Freeman, 1994), pages 132-139.
(43) “T-rail” is the type of rail still used today. It has a wide, flat top and a narrow bottom, like a T, that fits securely into chairs spiked onto the ties of the track. It replaced “strap rail” which consisted of flat bars of iron spiked to the top edges of wooden beams called stringers. T-rail can carry much heavier loads than strap rail. It is made by passing iron or steel ingots through a series of dies, or rollers, that progressively shape it.
(44) Anthracite Trust (Freeman, 1994), page 150-151.